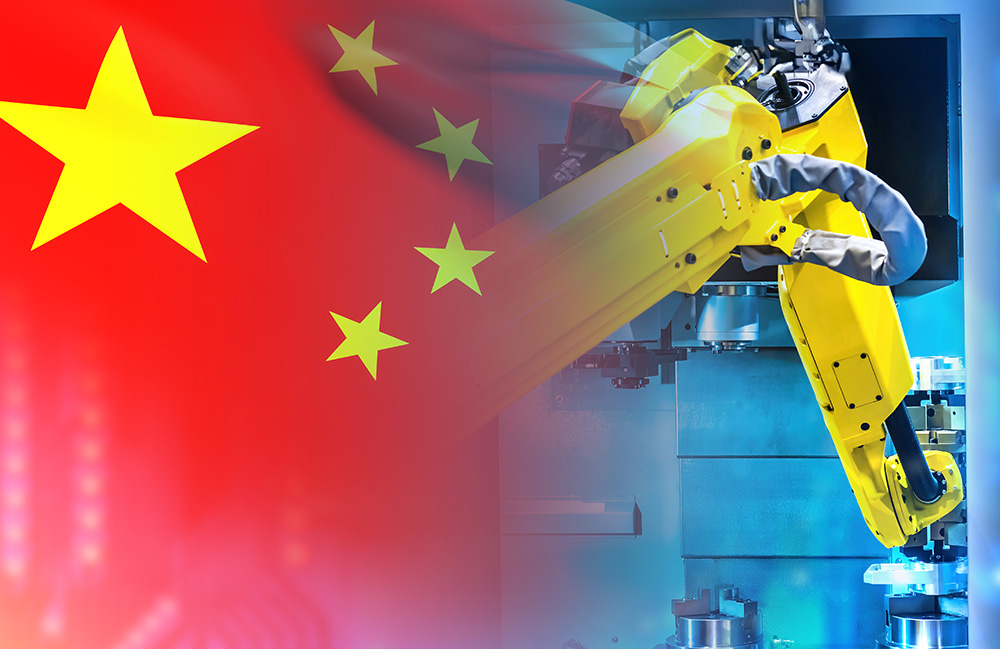
In 2023, China surpassed Germany and Japan in robot density, with 470 robotics per 10,000 employees, according to the International Federation of Robotics.|Source: Adobe StockThe U.S.
is falling behind in its efforts to reshore manufacturing, and among the most significant challenges is hiding in plain sight: a lack of mechanical engineers.
While China finishes more than 350,000 mechanical engineers each year, the U.S.
produces less than 45,000.
That’& rsquo; s not simply a gap in numbers-- it’& rsquo; s a structural downside that might limit our ability to scale industrial development.
And that doesn’& rsquo; t even include other vital fields of engineering like industrial, controls, and manufacturing, which are simply as crucial to the future of U.S.
manufacturing.I’& rsquo; ve worked in robotics and automation for more than 20 years, across nationwide research laboratories, start-ups, and open-source efforts.
In every context, the equation has actually remained the very same: You require individuals and tools, competent engineers to design and incorporate solutions, and automation that allows small groups to scale their impact.If we’& rsquo; re serious about bringing manufacturing back to the U.S., we can’& rsquo; t concentrate on policy alone.
We need a national method that purchases both STEM education and practical, scalable robotics automation.Gap in engineers undermines reshoring from ChinaMechanical engineers are fundamental to manufacturing.
They create the systems, fix the integration, and link software application to physical execution.
But as education costs rise and public perception of manufacturing remains out-of-date, fewer trainees are pursuing engineering professions.
And too couple of understand the effect these functions have on worldwide competitiveness.Meanwhile, other nations are taking a viewpoint.
China’& rsquo; s financial investment in engineering education covers universities, trade schools, and government-backed apprenticeships.
That sort of national pipeline develops commercial capability that scales.In the U.S., we need a comparable strategy.
That indicates early STEM engagement, more accessible engineering degrees, and programs that highlight what modern manufacturing in fact appears like—-- automated, precise, and significantly software-defined.
Conserve now with early bird discountRobots won’& rsquo; t replace individuals-- they & rsquo; ll assist us scaleAutomation isn’& rsquo; t about replacing jobs.
It’& rsquo; s about enabling engineers and technicians to achieve more with less.
This is particularly real for small and midsize producers, which often do not have the resources to build large teams or deploy innovative systems on their own.Throughout my profession, I’& rsquo; ve seen how the right automation platform can multiply the output of a single engineer.
However I’& rsquo; ve likewise seen how unattainable those tools can be.
Smaller sized manufacturers are frequently neglected of the automation conversation—-- not due to the fact that the requirement isn’& rsquo; t there, but because the cost, intricacy, and technical requirements are still too high.That’& rsquo; s among the reasons I helped launch ROS-Industrial over a decade earlier—-- to make robotics more open, modular, and scalable.
Open-source just goes so far without education, training, and support.
We need policies that deal with all three.Why now?Despite years of reshoring rhetoric, trade policy alone hasn’& rsquo; t delivered a significant revival.
Factory output has actually stayed unequal, supply chains are still susceptible, and many little and midsize producers lack the workforce and innovation to scale.
Meanwhile, worldwide rivals have invested strongly in automation, infrastructure, and technical education—-- building not simply capability, however resilience.At the same time, the U.S.
has fallen behind in preparing for the truths of a new labor economy.
Automation is no longer a future idea—-- it’& rsquo; s a contemporary requirement.
Adoption stays fragmented, and upskilling efforts sanctuary’& rsquo; t kept rate with industry needs.If we wear’& rsquo; t act now-- while reshoring momentum is real and bipartisan assistance exists—-- we run the risk of missing out on a narrow window of chance.
Other countries such as China are currently constructing the systems and workforce to dominate the next period of commercial development.
This isn’& rsquo; t just about jobs.
It & rsquo; s about maintaining strategic capability, accelerating efficiency, and securing long-term economic resilience.Invest in both individuals and toolsThe future of American production depends upon 2 things: people and the tools that empower them.
That indicates rethinking how we fund STEM education, broadening access to engineering careers, and making automation practical for the producers who need it most.Reshoring won’& rsquo; t prosper if we deal with education, workforce advancement, and robotics as different discussions.
They’& rsquo; re deeply interconnected.
We require mechanical engineers to create the systems, and we require automation to help them scale.
Without both, we’& rsquo; ll continue to disappoint our commercial goals.About the authorShaun Edwards is the co-founder and primary innovation officer of Plus One Robotics, a venture-backed start-up releasing robotics in logistics and e-commerce.
He forms the company’& rsquo; s technical vision, item roadmap, and software application architecture.Previously, Edwards was a principal engineer at Southwest Research Institute (SWRI), where he led research study and development and released automation throughout markets like aerospace, food, and logistics.
Shaun likewise founded the ROS-Industrial open-source project, now an international effort supported by significant robotics companies.
He holds an M.S.
in mechanical engineering from Case Western Reserve University.The post America can’& rsquo; t out-innovate China without mechanical engineers —-- or robots appeared initially on The Robot Report.