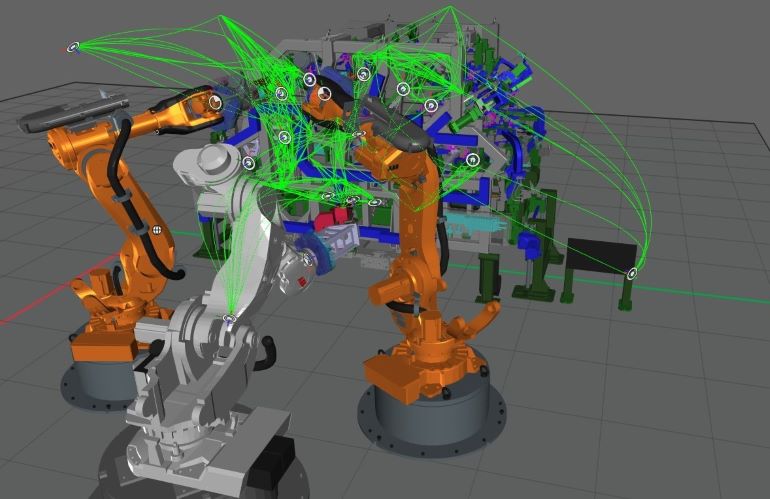
Realtime Robotics automates and optimizes motion planning with Resolve.
Source: Realtime RoboticsDETROIT — Robot path planning is traditionally a complex, time-consuming, and brittle process, according to Realtime Robotics.
The company today launched Resolver, a cloud-based motion control system that it said can accelerate the design and deployment of robotic workcells.Many workcells use multiple robots, and avoiding collisions during production processes often requires tedious manual labor to create interference zones and interlock signals.
Manually validating the mechanical design, planning robot paths, determining sequencing to hit optimal cycle time targets, and defining those interlocks can take a team more than 100,000 hours for a single project.The complexity often leads to failures in hitting cycle-time targets, adding expensive rework to 10% to 15% of workcells, noted Realtime Robotics.“It is widely understood that the future of the manufacturing industry lies in robotics and automation,” stated Peter Howard, CEO of Realtime Robotics.
“However, that future is slow to materialize because of the outdated, time-consuming, and inefficient processes commonplace in the industry.”“Few manufacturers have the time or resources needed to enact real change,” he added.
“We’ve engineered Resolver to help manufacturers improve their engineering, programming and production processes — and drive greater value from their current and future investments in robots.”The Resolver simulation software interface from Realtime Robotics.
Click here to enlarge.
Source: Realtime RoboticsResolver applies simulation for workcell safetyBoston-based Realtime Robotics claimed that it is the leader in automated collision-free motion planning, control, and optimization for industrial robots.
The company said it solves for cycle-time optimized motions, interlocks, multi-robot coordination, real-time object detection and reaction, and robot-to-task allocation.Resolver selects and tests potential solutions tens to thousands of times faster than any human programmer, quickly generating optimal motion paths and interlock signals, asserted Realtime.With Resolver, organizations can automatically discover the fastest target order, accelerating workcell design from months to days while also decreasing engineering effort by 50%, the company asserted.
“Workcell cycle times are reduced, and overall throughput is increased,” it said.Realtime Robotics does more than just path planning, said Ville Lehtonen, who became vice president of product in November.“When we think of path planning, we often forget everything that goes into making a functional robotic cell,” he told The Robot Report.
“What Realtime’s Resolver does isn’t so much path planning — though that is certainly important — as it is a virtual simulation engineer.”“A great deal of a simulation engineer’s work has little to do with path planning — and much more with helping mechanical design,” Lehtonen said.
“‘Can this weld gun reach all these targets without collision?’ ‘Should I put six or seven robots in this cell, and where should I place them?’ ‘Hey, I’ve made this fixture, are you guys OK with it, given the weld gun you’re using?’ ‘Which cells could take over some re-spot welds from this workcell?’”“These are the common questions and issues a simulation engineer deals with every day,” he added.
“The problem with answering these isn’t always the complexity of the task; it’s the sheer volume of such work.”“Resolver not only allows you to answer all of these questions automatically; it will do the path planning as well, meaning that instead of yes/no answers, engineers can get answers with an estimated cycle time,” explained Lehtonen.
“‘Yes, both weld guns A and B work, but A allows us to be 25% faster’ is a rather valuable response for a simulation engineer to be able to share.Scalability and more support comingRealtime Robotics said Resolver “gives users affordable, on-demand, infinitely scalable robotic simulation power.”“Resolver supports path planning with any number of robots, at any phase of the workflow, generating results in minutes,” said Realtime Robotics.
“The solution requires minimal onboarding — and currently allows users to work directly within Siemens Process Simulate.”The company plans to roll out support for other leading simulation platforms later in the year, enabling teams to work directly within their preferred simulation tools.“Resolver has the computational power to generate better motion paths than human programmers in both simple and complex workcells,” Howard said.
“This is because Resolver searches the possibilities open to robotic arms, while humans tend to stay within the possibilities of the human arm.”Resolver promises to accelerate motion planning for robotics application development.Design users can see rapid returnsTo get started with Resolver, users just need to upload the workcell information into a new project, configure their sequencing and conditions, and execute a run.
In minutes, Resolver can generate motion paths, including interlocks, with a superhuman cycle time, said Realtime Robotics.The longer Resolver runs, the more options it provides, shortening the cycle time until the desired outcome is reached.
The paths and interlocks can then be easily imported back into the simulation software for validation and operation, the company said.The system is hardware-agnostic and currently supports major robot brands, Lehtonen added.
It also provides human support.“Resolver eliminates the most time-consuming aspects of industrial robotics — the programming and optimization of the robots.
What used to take months to accomplish can now be measured in hours,” observed Marco Bizjak, head of Competence Center Digital Factory and technical manager for digitalization at FFT.
“We believe this can be a real competitive advantage as we strive to help our customers establish the most efficient and effective manufacturing processes possible.”Resolver also has enhanced features, allowing it to be used at any point in the project lifecycle, from proposal to workcell design, Realtime said.
It said the product can facilitate more accurate cycle-time estimates, enabling organizations outbid the competition during the proposal process.In addition, Realtime said it can shorten the design phase by streamlining manual path planning into simple steps, automatically defining interlock signals and minimizing mechanical design iterations.“The assistance comes in the very early stages of the design cycle, when you’re just putting the cell together,” noted Lehtonen.
“Or even before it, when you’re evaluating a customer project with a particularly tight cycle time.
Without much work at all, Resolver can tell you that this cell will be 52 seconds against a target of 60 seconds, which should leave plenty of room for tweaks during commissioning.”In addition, Resolver can help with fixture design, reachability validation, target sequencing, and robot task allocation.
It can also be used to design the paths and interlocks for an entire manufacturing line from the start, giving an organization a comprehensive view of its entire operation, said Realtime Robotics.Realtime Robotics to exhibitRealtime Robotics will show how Resolver can help organizations improve their engineering and manufacturing efficiency at two trade shows:Automate 2025, May 12-15 in Detroit: Realtime will be in Booth 9101 in Hall E.Automatica 2025, June 24-27, in Munich, Germany: The team will be in Booth 301 in Hall B6.“Resolver is now available and ready for use,” Lehtonen said.
“Those interested can request access today to a free Resolver demo environment at https://rtr.ai/demo/.
Resolver is a cloud-based SaaS [software-as-a-service] solution, meaning you can be up and running before the day is over.
Sign up, log in, download and install the connector for your simulator, load up your workcell, and simply hit ‘Resolve.’”
Now accepting session submissions!
The post Realtime Robotics launches Resolver for motion planning, simulation appeared first on The Robot Report.